By Weedsmart’s Cindy Benjamin
Weed detection and spot spraying in fallow is a powerful way to reduce chemical use, conserve soil moisture and run down the weed seed bank.
Andrew and Cynthia Pursehouse along with eldest son James recently employed a Swarm Bot named Mooki, fitted with a13m RBE boom and Weed-IT Quadro sensors as a dedicated fallow spot-spraying unit on their 5100 hectare mixed farming operation, Breeza Station, on the Liverpool Plains in NSW.
In 2015, they began optical spot spraying using a 36mWeedseeker boom on their Miller Nitro SP to reduce chemical use in fallow fields.
Spot spraying fallow weeds, including milk thistle, fleabane, ryegrass, windmill grass, and barnyard grass, uses much less chemical per spray pass than blanket spraying, representing significant savings to their business.
James says although the 36m Weedseeker boom worked well, they frequently needed their self-propelled machine to do two jobs simultaneously.
The family investigated their options and weighed the pros and cons of buying a second self-propelled sprayer or an autonomous (robot) to increase their spray capacity.
“While both are expensive pieces of machinery, we saw the benefit of the robotic option as the ability to do two spray jobs simultaneously without needing to employ an extra operator,” he says.
In 2022, they ordered a robotic platform from SwarmFarm as a dedicated fallow weed spot-spraying unit, and it was deployed on Breeza Station in June 2023.
“In the 14 months between June 2023 and August 2024, the Swarmbot completed 1490 engine hours, which includes time travelling, spraying and in sleep mode,” James says.
“It has an average operating speed of 9.7 ha/hr, uses 0.8 L/ha of diesel, and has a running cost of $4/ha.”
In comparison, their SP sprayer typically covers 50 ha/hr and uses 0.9 L/ha of diesel when camera spraying, giving a similar running cost per ha. It also requires a driver.
James says they have made a major shift from reactive to proactive weed management, where they are now targeting smaller weeds more often using a spray rotation of three to four weeks, according to weather conditions.
“All weeds are more susceptible to herbicide when they are small,” he says.
“The robot removes the normal temptation to hold o spraying to wait for a few more weeds to emerge.
“The fact the robot will return to each paddock within a few weeks means we are continually driving down the weed seedbank by eliminating small weeds before they can establish and set seed.
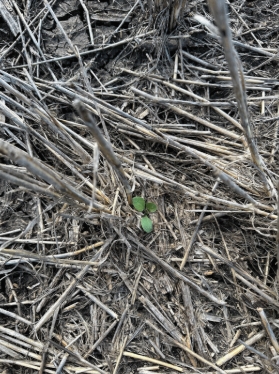
The family have implemented many of the WeedSmart Big 6tactics to reduce their risk of herbicide resistance, including increasing their spray efficacy with the robot providing a consistent 50cm boom height and slower operating speed so the Weed-IT sensors can detect very small weeds in heavy stubble.
To comply with their controlled traffic system, Mooki has 4m centres and a 13m RBE spray boom. This is standard for12m CTF systems to provide a 0.5m overlap for each pass. The platform carries a 1500L spray tank and weighs about 5twhen fully loaded.
“The Nitro SP weighs about 20t when fully loaded, so the robot has a distinct advantage when it comes to minimising compaction and getting onto paddocks sooner after rain,” James explains.
“We selected 1400mm high-clearance chassis so we didn’t lock ourselves out of future use opportunities such as inter-row spraying in skip-row cotton crops.”
Since adding Mooki to the farm workforce, the self-propelled sprayer’s engine hours have been reduced, extending its effective life. Staff time and skills have also been better utilised.
“At cotton picking time, the whole team can focus on picking and mulching jobs knowing that Mooki is attending to the fallow spraying,” he says.
“This means all jobs are being done on time, and we don’t have to worry about the fallow weeds depleting our stored soil moisture or setting seed. And none of us wish we were out spot spraying.”